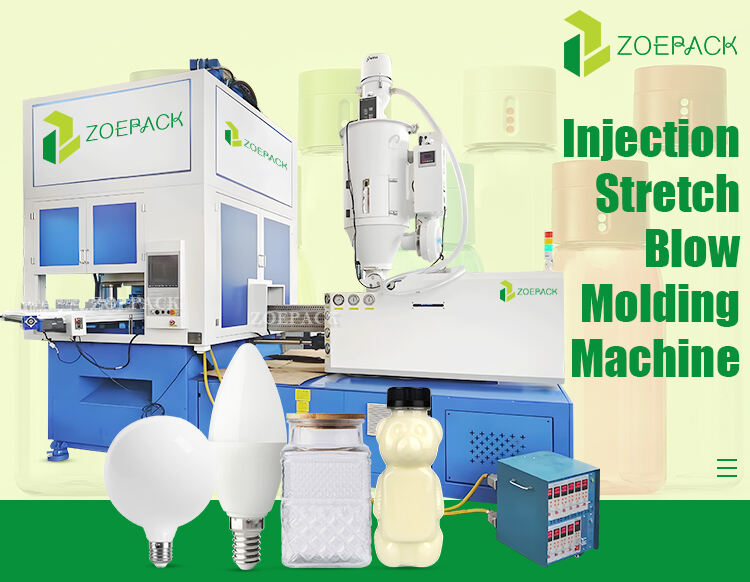
Energy - Efficiency of Injection Stretch Blow Molding Machine
In an era where environmental sustainability and cost - effectiveness are top priorities in manufacturing, the Injection Stretch Blow Molding Machine stands out for its remarkable energy - efficiency.
The one - step nature of the ISBM process is a key factor in its energy - saving capabilities. By integrating injection, stretching, and blow molding into a single continuous operation, the machine eliminates the need for multiple heating and cooling cycles that are typical in traditional manufacturing methods. In traditional setups where each process is carried out separately, the plastic material has to be heated multiple times, first for injection, then reheated for blowing. This repeated heating consumes a significant amount of energy. In contrast, the ISBM machine optimizes the energy usage by heating the plastic only once in the injection stage and then using the residual heat and carefully controlled heating during the stretching and blowing stages.
The precise temperature control systems in the ISBM machine also contribute to energy - efficiency. The heating elements in the barrel, hot runner, and heating station are equipped with advanced sensors and controllers. These devices monitor the temperature in real - time and make precise adjustments to maintain the optimal temperature for each stage of the process. By ensuring that the plastic is heated to exactly the required temperature and not over - heated, energy waste is minimized. For example, in the heating station where the preform is reheated, the mica heat rings can be adjusted to provide just the right amount of heat to make the preform malleable for stretching and blowing, without using excessive energy.
Another aspect of energy - efficiency in the ISBM machine is its efficient use of compressed air. During the blow - molding stage, high - pressure air is used to expand the preform into the shape of the mold. The machine is designed to optimize the air pressure and flow rate, ensuring that the minimum amount of compressed air is used to achieve the desired results. This not only saves energy but also reduces the wear and tear on the air - compression equipment, leading to lower maintenance costs.
In addition, the compact design of the ISBM machine plays a role in energy - conservation. The smaller footprint of the machine means that there is less surface area to heat or cool in the factory environment. This reduces the overall energy consumption required to maintain a suitable working temperature in the production area.
Furthermore, many modern ISBM machines are equipped with energy - recovery systems. These systems capture and reuse the heat generated during the manufacturing process. For example, the heat from the cooling of the molded products can be used to pre - heat the incoming plastic resin pellets or to warm the factory premises. This further enhances the energy - efficiency of the machine and reduces its overall carbon footprint.
In conclusion, the Injection Stretch Blow Molding Machine offers significant energy - saving advantages. Its integrated process, precise temperature control, efficient use of compressed air, compact design, and energy - recovery systems make it a sustainable choice for manufacturers looking to reduce their energy consumption and operating costs while maintaining high - quality production.
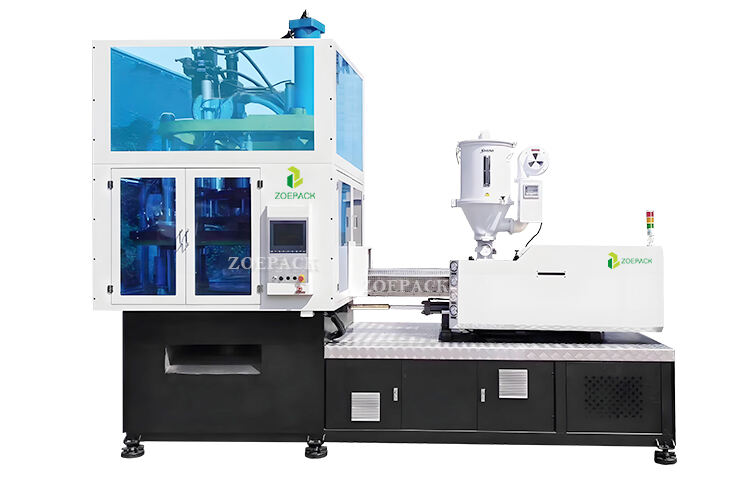
Injection Part |
Screw Diameter |
40mm |
Screw L/D Ratio |
20.5:1 |
Screw Speed |
0-190RPM |
Theoretical Injection Capacity |
238cm3 |
Injection Pressure |
174Mpa |
Max. Hydraulic Pressure |
|
The Actual Injection Quantity(PS): |
|
Screw Stroke: |
|
Clamping Part |
Blow Clamping Force: |
800 |
Clamp Tonnage: |
400Kn |
Wheel Diameter: |
800mm |
Max. Height of Bottle: |
ISB: 145 / one: 140 |
Open Vertical Mode Trip: |
430mm |
Others |
Max. Pump Pressure: |
16Mpa |
Motor Oil: |
18.5Kw |
Electric Power: |
12.2Kw |
Oil Tank: |
400L |
Overall Dimension(L*W*H): |
3.8M * 1.45M * 3.0m |
Weight: |
5000kg |
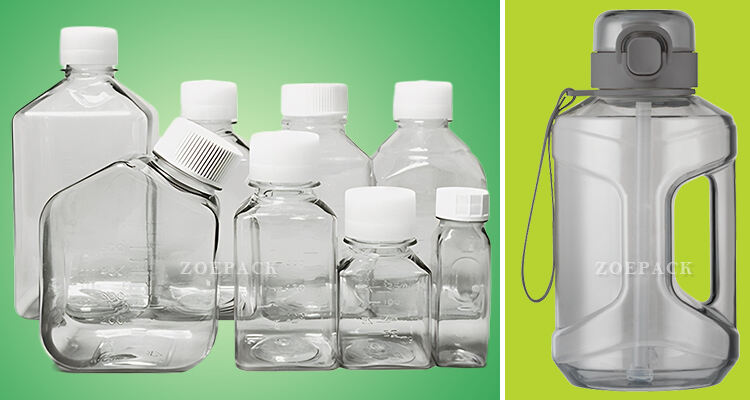
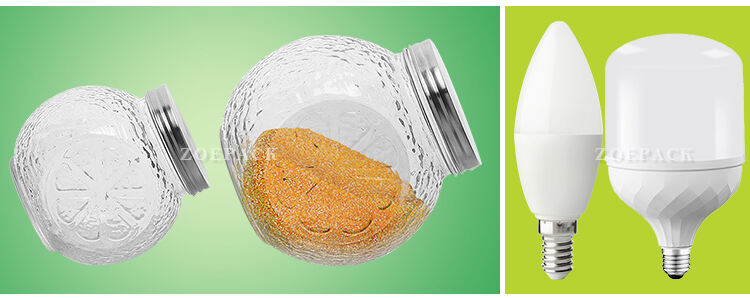
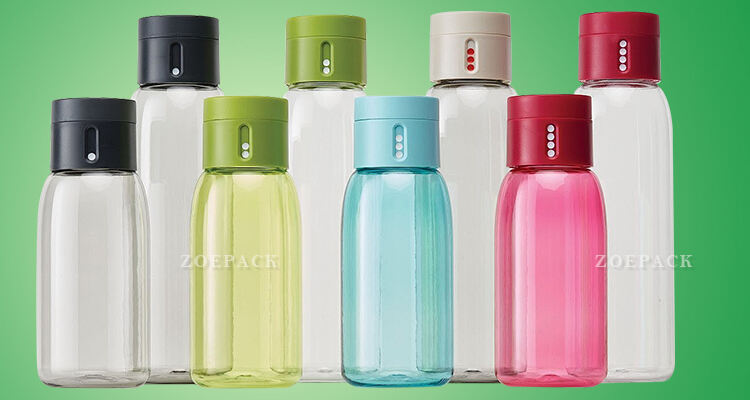
ISB800 |
PC, PS,PMMA lamp cover, LED light lampshade,Christmas flash light, garden and street light. |
PET high transparent bottle(thinner wall), cosmetic bottle 10ml to 500ml, PET wide neck jar, PET pharmaceutical bottle. |
PP high transparent bottle, baby feeding bottle, sport bottle |
PCTG, Tritan drinking water bottle, sport bottle |
Single step VS Two-step Single step and two-step
Molding |
Process |
Structure |
Manpower/Energy/Space |
Product Quality |
Dawson One-step Injection Stretch Blow Molding Machine |
From preform to product in one machine |
One machine |
Little |
Not affect by damp and less pollution; Various kinds of shape |
Other machine |
Injection and blow molding are two separated process |
1.Injection molding machine 2.Preform transiting machine 3.Reheating, stretch and off-moulding machine |
More |
Easy affect by damp and polluted; Singleness shape |
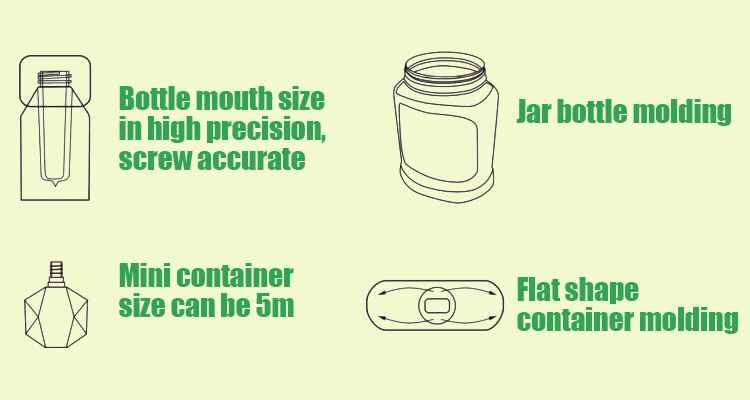

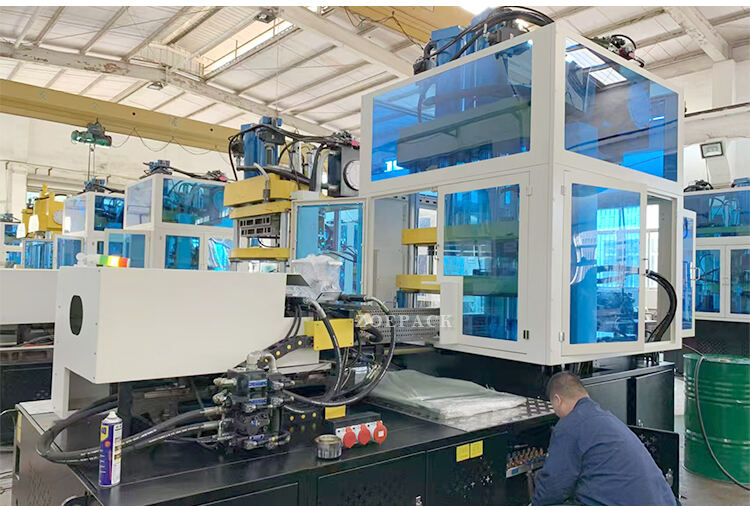
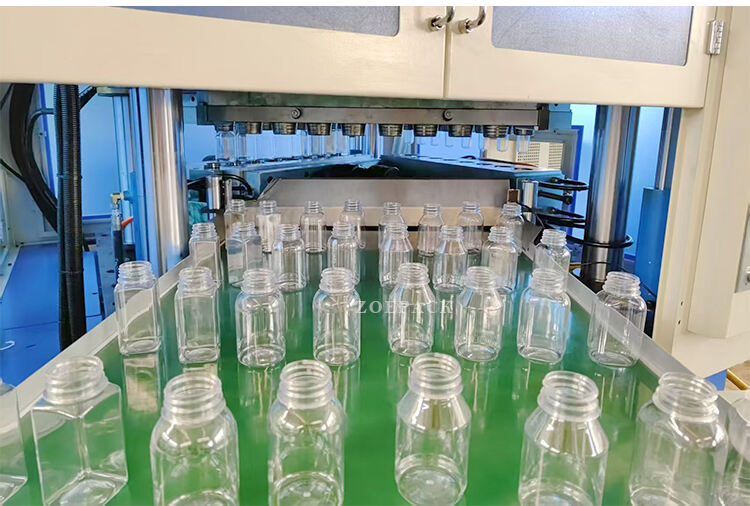
1. The wheel rotation is driven by electrical servo motor, not hydraulic.
2. Full automatic controlling system, easy operating.
3. The temperature of material barrel and hot runner is controlled accurately by PIT.
4. More cost is saved than traditional machine.
5. Compact structure; less space needed.
6. Injection: Hot runner and temperature control device are standard configuration.
Only change mold for making a new product;
Stretch Blow: Hydraulic mold clamping, core insert, stretch blow and bottom molding are standard configuration;
Product Release: Equipped with a standard ejector.
ZOE PACK
located in Zhangjiagang city, have more than 18 years' experience in the field of plastic machinery, injection molding machine, blow molding machine, PET blow molding machine, injection blow molding machine, during the past 18 years, we always force our energy into new areas of plastic machinery, plastic packaging machinery, to update the technology, to learn advanced experience,to confirm new theory and new design, we are forming a unique competitive advantage of our owns.The machines from our company carry good quality and effective after-sales service, upon the market,
customers from more than 45 countries, we provide complete solution for your plastic industry business, as well as all sorts of technical support & after-sale services!
ZOE PACK will be your reliable friend in China, and we will always do our best to give you max support!