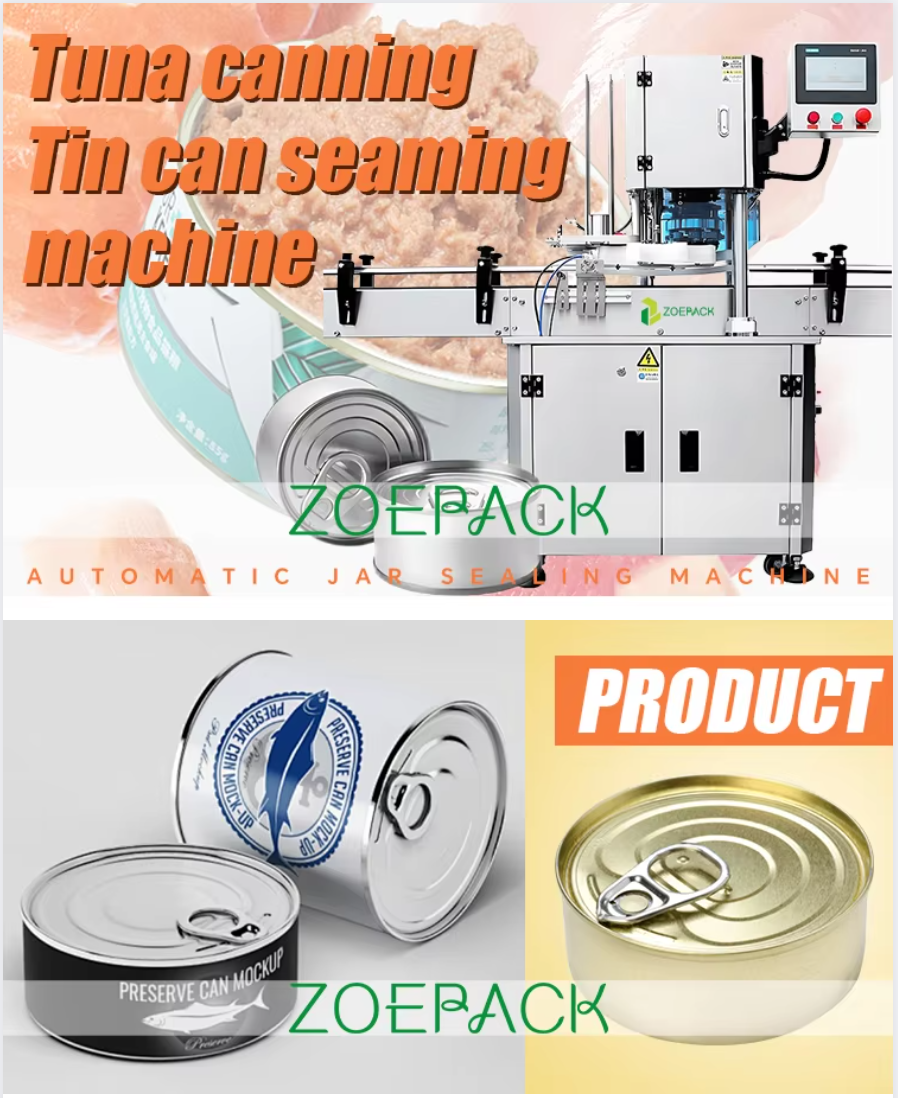
Applications
Number of sealing head |
1 |
Number of seaming rollers |
4(2 frst operation,2 second operation) |
Sealing speed |
35~50 cans/ min(adjustable) |
Sealing height |
25-220mm |
Sealing can diameter |
35-130mm |
Working temperature |
0-45℃ |
working humidity |
35~85% |
Total power |
2.1KW |
Weight |
330KG |
Dimensions |
L1850* W 840*H1650mm |
Features
The Revolutionary Automatic Jar Sealing Machine
In the fast - paced world of modern manufacturing and packaging, the demand for high - quality, efficient, and reliable equipment is ever - increasing. The Automatic Jar Sealing Machine has emerged as a game - changer in the packaging industry, offering a plethora of advanced features that set it apart from traditional sealing methods.
Whole Machine Servo Control: Stability and Intelligence Redefined
The Automatic Jar Sealing Machine is equipped with whole machine servo control, which is a technological marvel. Servo control systems are known for their precision and ability to provide smooth and stable operation. In the context of the jar sealing machine, this means that every movement of the machine is carefully regulated. The servos can accurately control the speed, position, and torque of various components, ensuring that the sealing process is consistent and flawless.
This stability is crucial for maintaining the quality of the sealed products. For example, in the food and beverage industry, where the integrity of the seal is directly related to the shelf - life of the product, a stable sealing process can prevent leaks and contamination. The intelligence of the servo - controlled system also allows for easy programming and customization. Operators can set different parameters for different types of jars, such as size, shape, and the type of lid, and the machine will adjust its operation accordingly. This flexibility makes the Automatic Jar Sealing Machine suitable for a wide range of applications, from small - scale artisanal production to large - scale industrial manufacturing.
Turntable Operation: Energy - Efficiency and Smart Functionality
One of the unique features of this machine is that the turntable only runs when there is a can present. This is an energy - saving and smart design. In traditional can - sealing machines, the turntable often runs continuously, consuming unnecessary energy. By implementing a sensor - based system that detects the presence of a can, the Automatic Jar Sealing Machine reduces power consumption and also minimizes wear and tear on the machine components.
This feature also enhances the overall efficiency of the production line. Since the turntable only activates when needed, there is no wasted motion or time. This is particularly beneficial in high - volume production environments where every second counts. For instance, in a factory that produces thousands of jars of preserves daily, the energy savings from this feature can be substantial over time. Additionally, the reduced wear on the turntable means less frequent maintenance and replacement of parts, leading to lower operational costs.
One - Button Reset: Simplifying Operation and Maintenance
The one - button reset feature of the Automatic Jar Sealing Machine is a boon for operators. In any complex machinery, there may be times when the machine needs to be reset due to a minor malfunction or a change in the production process. With the one - button reset, this process is simplified to the extreme.
This not only saves time but also reduces the risk of human error. In a busy production environment, operators may be under pressure to quickly resolve issues. The one - button reset ensures that the machine can be brought back to its default or a pre - set state with just a single press. This is especially useful for less - experienced operators who may not be familiar with complex troubleshooting procedures. From a maintenance perspective, it also makes it easier for technicians to diagnose and fix problems. If a problem occurs, they can first use the one - button reset to see if the issue is a minor glitch. If the problem persists, they can then delve deeper into the machine's systems for more comprehensive repairs.
Four Seaming Rollers: Unparalleled Sealing Performance
The Automatic Jar Sealing Machine is designed with a total of 4 seaming rollers that complete the sealing process simultaneously. This configuration significantly enhances the sealing performance. Each seaming roller plays a specific role in the process, working in harmony to create a tight and secure seal.
The use of multiple rollers allows for a more uniform application of pressure around the circumference of the can. This results in a seal that is not only strong but also consistent across all jars. In industries such as pharmaceuticals and cosmetics, where product integrity is of utmost importance, the high - quality seal provided by the 4 - roller system is essential. It can prevent the entry of air, moisture, and other contaminants, thus preserving the quality and efficacy of the products inside the jars. The high - sealing performance also reduces the likelihood of product recalls due to faulty seals, which can be costly for manufacturers in terms of both reputation and finances.
Stationary Can Body: Safety and Suitability for Fragile and Liquid Products
During the sealing process, the can body remains stationary in the Automatic Jar Sealing Machine. This is a safety - focused design that offers several advantages, especially for fragile and liquid products. For fragile items, such as glass jars with delicate contents, the stationary can body prevents any potential damage that could occur if the can were to rotate.
In the case of liquid products, a non - rotating can body ensures that the liquid remains evenly distributed inside the can. This is important because if the liquid were to slosh around during the sealing process, it could affect the quality of the seal. For example, in a winery, where the wine needs to be sealed in glass bottles, the stationary can - body design ensures that the wine does not spill or cause any interference during the sealing operation. The safety aspect is also crucial in a production environment, as it reduces the risk of accidents caused by moving cans. Operators can work more comfortably and with less risk of injury, knowing that the cans are not in motion during the sealing process.
High Sealing Speed: Meeting the Demands of Mass Production
The Automatic Jar Sealing Machine has an impressive sealing speed of up to 50 cans per minute. This high - speed operation makes it an ideal choice for large - scale production facilities. In industries such as food and beverage, where the demand for products is constantly high, the ability to seal a large number of cans in a short period is essential.
For example, a soft - drink bottling plant may need to seal thousands of cans of soda every hour. The high - speed Automatic Jar Sealing Machine can easily keep up with such production requirements. This not only increases the overall productivity of the plant but also allows manufacturers to meet market demands more efficiently. With a faster sealing speed, companies can reduce their production time and costs, as they can produce more products in less time. This gives them a competitive edge in the market, allowing them to offer their products at more affordable prices or increase their profit margins.
Transparent Blue Acrylic Cover: Aesthetic Appeal and Safety
The transparent blue acrylic cover of the Automatic Jar Sealing Machine serves multiple purposes. Firstly, it adds to the aesthetic appeal of the machine. In a modern factory setting, where appearance can matter, the blue cover gives the machine a sleek and professional look.
Secondly, and more importantly, it provides multiple protection. The cover acts as a physical barrier, preventing operators from accidentally coming into contact with moving parts of the machine. This significantly reduces the risk of injuries in the workplace. In addition, the transparency of the cover allows operators to monitor the sealing process without having to open the machine. They can easily see if there are any issues, such as misaligned cans or problems with the sealing rollers, and take immediate corrective action. This combination of beauty and safety makes the Automatic Jar Sealing Machine a top choice for manufacturers who are looking for both functionality and a visually appealing addition to their production lines.
In conclusion, the Automatic Jar Sealing Machine with its advanced features of whole machine servo control, intelligent turntable operation, one - button reset, 4 - seaming - roller high - performance sealing, stationary can - body design, high sealing speed, and protective transparent blue acrylic cover is revolutionizing the packaging industry. It offers a perfect blend of efficiency, safety, and quality, making it an indispensable tool for manufacturers across various sectors.
Company Profile
ZOE PACK
located in Zhangjiagang city, have more than 18 years' experience in the field of plastic machinery,injection molding machine, blow molding machine, PET blow molding machine, injection blow moldingmachine, during the past 18 years, we always force our energy into new areas of plastic machinery,plastic packaging machinery, to update the technology, to learn advanced experience,to confirm newtheory and new desian, we are forming a unigue competitive advantage of our owns,The machines fromour company carry good quality and effective after-sales service, upon the market,customers from more than 45 countries, we provide complete solution for your plastic industry business,as well as all sorts of technical support & after-sale services!
ZOE PACK will be your reliable friend in China, and we will always do our best to give you max support!
FAQ
Q: Can we visit your factory?
Sure. We located in Zhangjiagang city which is very near Shanghai. For overseas customers, you canfly to Shanghai Pudong International Airport. We can pick you up in the Airport. (or HongqiaoInternational Airport. )We also provide visit online by video.
Q: How can we get the exact price of plastic machine?
Contact us with the products size, shape, annual quantity and photo if possible. We can recommendour machine models with quotation.
Q: Do you provide any spare parts with machine?
Yes, we offer all necessary spare parts before shipment.(contact us for packing list )
Q :How about your after-sale service ?
We offer manual instruction and engineer training before loading,after shipment we provide 24 HRS online support, video technical support or field installation assist.
Q: What is the lead time?
For customized machine, it takes about 45-50 days after deposit. Forstock machine, fast shipment. (The actual production cycle will vary according to the degree of customization.)
Q: What is the warranty period for your machine ?
12 months warranty for components and technical support.
Q: Do you provide custom machines?
Most of our machines are customized. Our goal is efficiency and stable performance. We design themachines according to customers products to meet customer' needs.
Q: How can we install the machine when it arrives?
We can send experienced technicians to customer's country for guiding the installation andcommission the machine, also train the customer's employees.
Q: What's ZOE PACK's advantage?
ZOE PACK provide customers with turnkey projects. Including plant design, plastic machine and moldinstallation, debugging, also we can source the auxiliary equipment for customers. We can ship the fullset of machines after testing in our factory. It will save a lot of cost and time.
ZOE PACK will be your reliable friend in china, and we will always do our best to give you max support!